Case Study: How a Georgia Factory Achieved Success with Lean Manufacturing
Introduction to Lean Manufacturing
Lean manufacturing is a systematic approach to minimizing waste without sacrificing productivity. Originating from the Japanese manufacturing industry, this methodology focuses on creating more value for customers with fewer resources. Recently, a factory in Georgia has exemplified how implementing lean manufacturing can lead to remarkable achievements.

The Georgia Factory's Background
Located in the heart of Georgia, the factory initially struggled with inefficiencies, high operational costs, and delayed production timelines. Like many manufacturing facilities, it faced challenges such as inventory excess, waiting time, and overproduction. The management realized the need for a transformation to stay competitive in a demanding market.
Embracing Lean Principles
To address these issues, the Georgia factory embraced lean principles. The foundation of this approach included:
- Identifying and eliminating waste
- Continuous improvement (Kaizen)
- Just-in-Time (JIT) production
- Standardized work processes
Implementing these principles required a cultural shift within the organization, involving training and engaging employees at all levels.
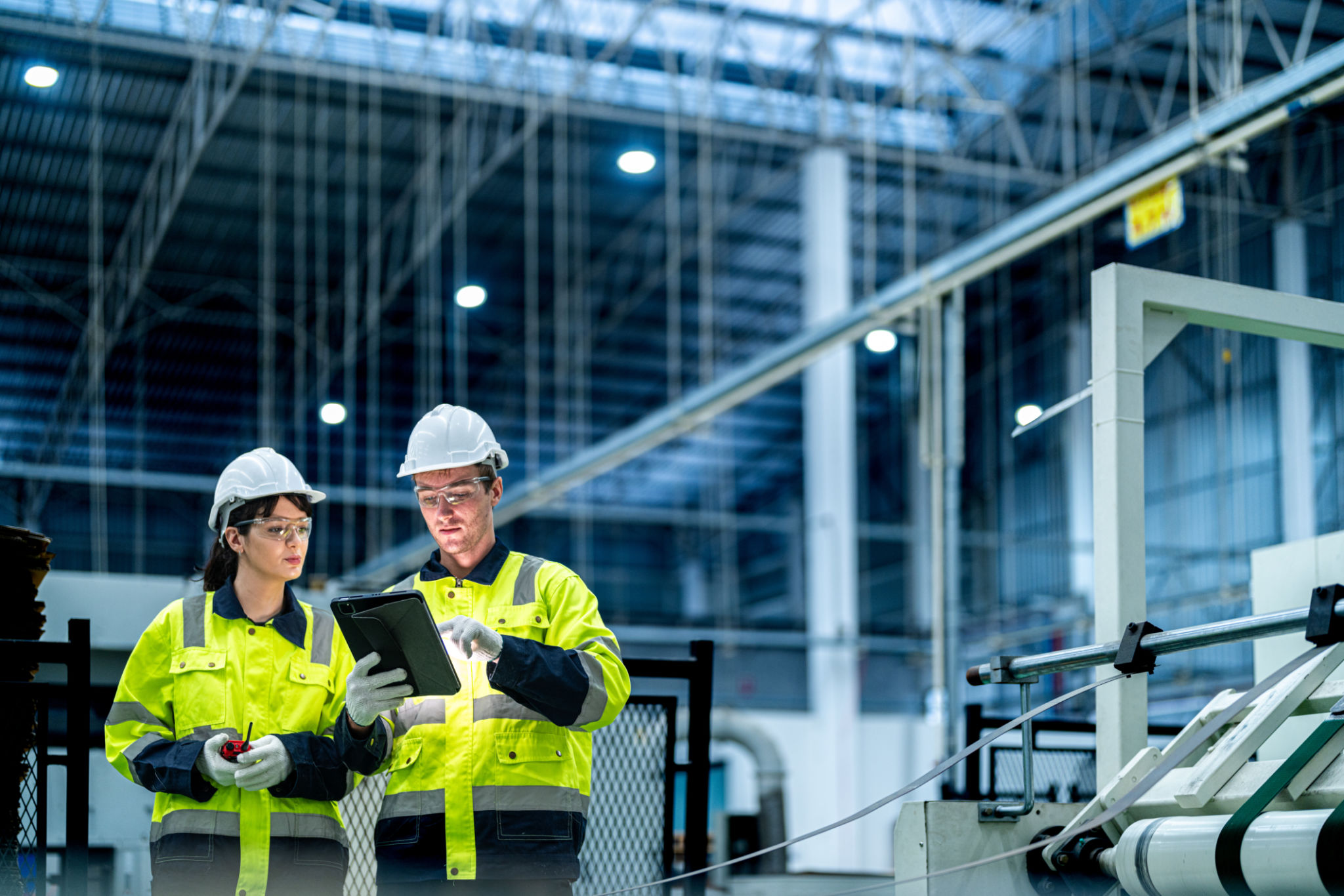
Implementation Process
The factory's management started by mapping out the entire production process to identify bottlenecks and waste. By focusing on value stream mapping, they could visualize areas needing improvement. Teams were formed to tackle specific issues such as reducing setup times and optimizing material flow.
One significant change was the adoption of Just-in-Time production, which reduced inventory costs and increased efficiency. By producing only what was needed when it was needed, the factory could better align its production with customer demand.
The Role of Technology
Incorporating technology was pivotal in the factory's lean transformation. Implementing software solutions for inventory management and production scheduling helped streamline operations. These tools provided real-time data, enabling quick decision-making and enhancing overall productivity.
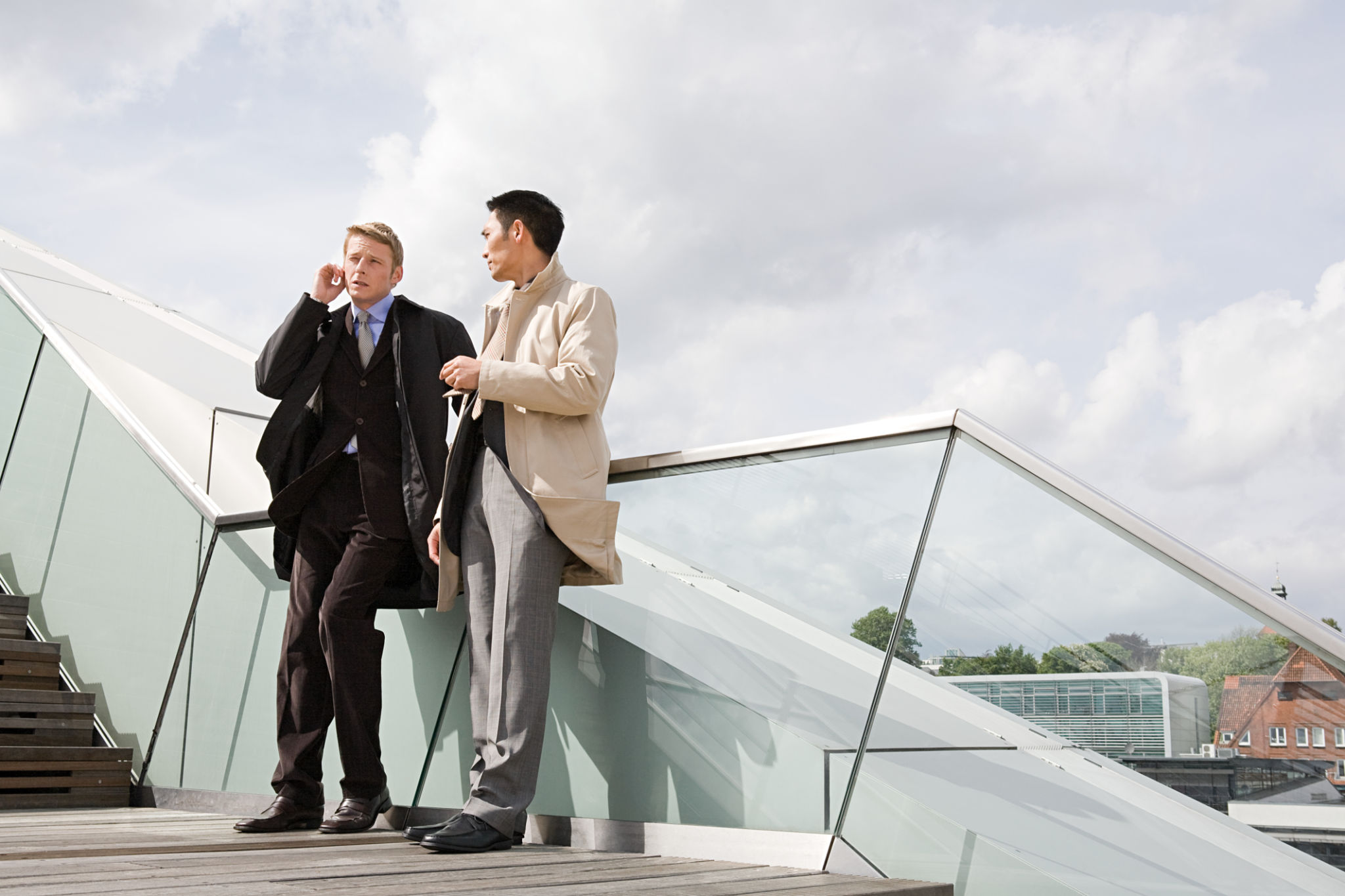
Results and Benefits
The results were impressive. The factory saw a significant reduction in lead times and a substantial decrease in waste. Operational costs dropped, and productivity soared. Employees were more engaged and motivated, leading to a better workplace environment.
Moreover, the factory's ability to deliver high-quality products on time improved customer satisfaction and loyalty, providing a competitive edge in the market.
Challenges Faced
Despite the success, the journey wasn't without its challenges. Resistance to change was a significant hurdle, as employees had to adapt to new methods and technologies. Continuous training and communication were crucial in overcoming these obstacles. Additionally, maintaining momentum for continuous improvement required ongoing commitment from management.
Conclusion
The Georgia factory's success story demonstrates how lean manufacturing can transform traditional production environments. By focusing on efficiency, waste reduction, and employee involvement, businesses can achieve substantial improvements in performance and profitability. This case study serves as an inspiring example for other factories aiming to harness the power of lean principles.