Case Study: Successful Digital Transformation in a Georgia Manufacturing Plant
Introduction
Digital transformation is more than just a buzzword; it's a crucial step for businesses aiming to stay competitive in today's rapidly evolving market. One Georgia manufacturing plant recently embarked on this journey and achieved remarkable success. This case study delves into the strategic steps taken by the plant to modernize its operations, the challenges faced, and the significant outcomes realized.
Understanding the Need for Change
The manufacturing industry has always been heavily reliant on traditional methods. However, with the rise of Industry 4.0, this Georgia-based plant recognized the urgent need to integrate digital technologies to optimize production and enhance efficiency. The initial phase involved a comprehensive assessment of their current processes and identifying areas ripe for improvement.
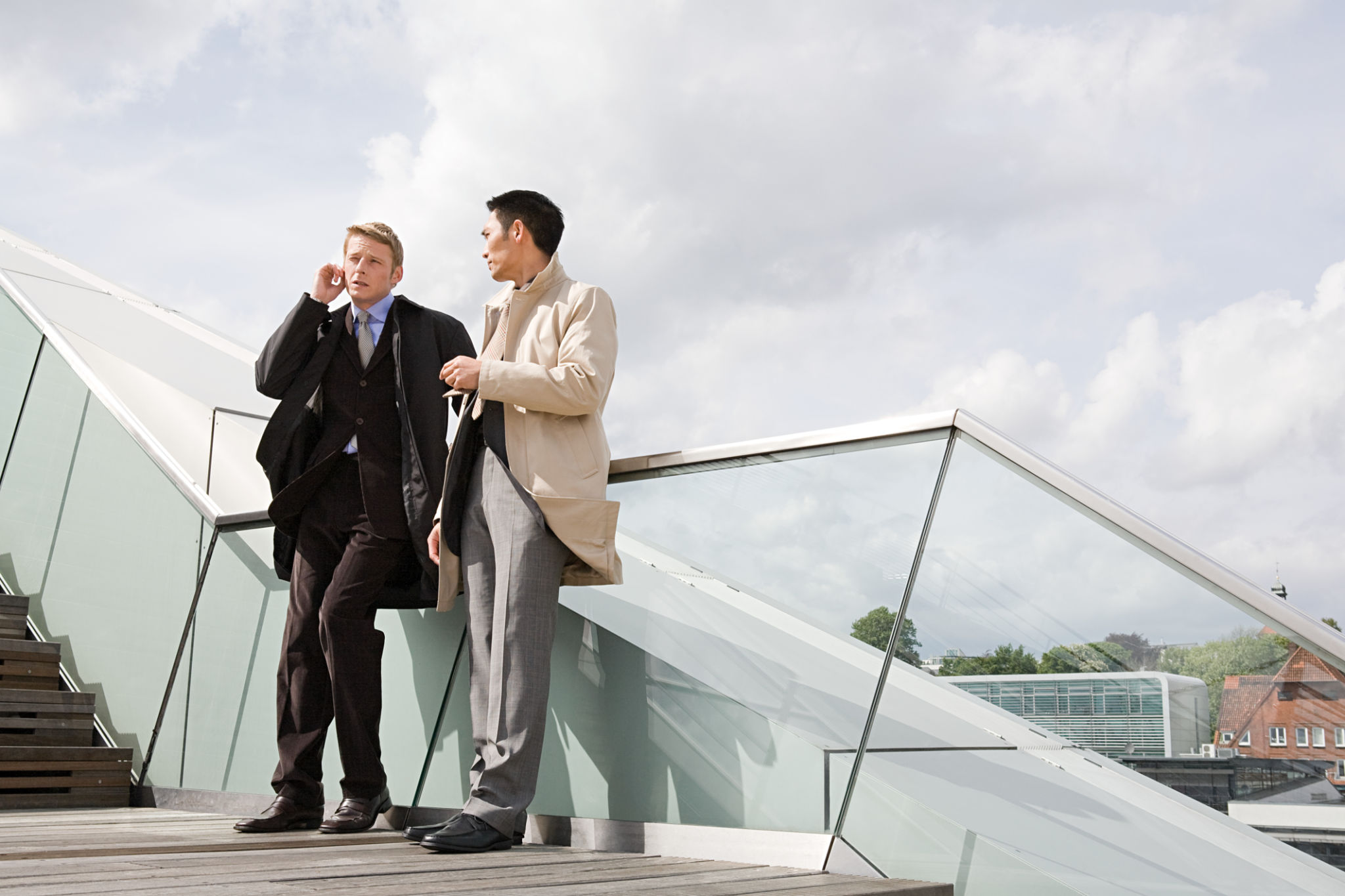
Challenges Faced
Embarking on a digital transformation is no easy feat. The plant faced several challenges, including:
- Resistance to Change: Many employees were accustomed to traditional methods, making them hesitant to adopt new technologies.
- Budget Constraints: Allocating sufficient funds to invest in cutting-edge technologies while maintaining ongoing operations was a significant hurdle.
- Data Integration: Integrating new software with existing legacy systems posed technical challenges.
The Transformation Journey
The plant adopted a phased approach to digital transformation, ensuring minimal disruption to ongoing operations. Key steps included:
- Implementing advanced data analytics for better decision-making.
- Adopting IoT solutions to improve machinery efficiency and maintenance schedules.
- Investing in employee training programs to enhance digital literacy.
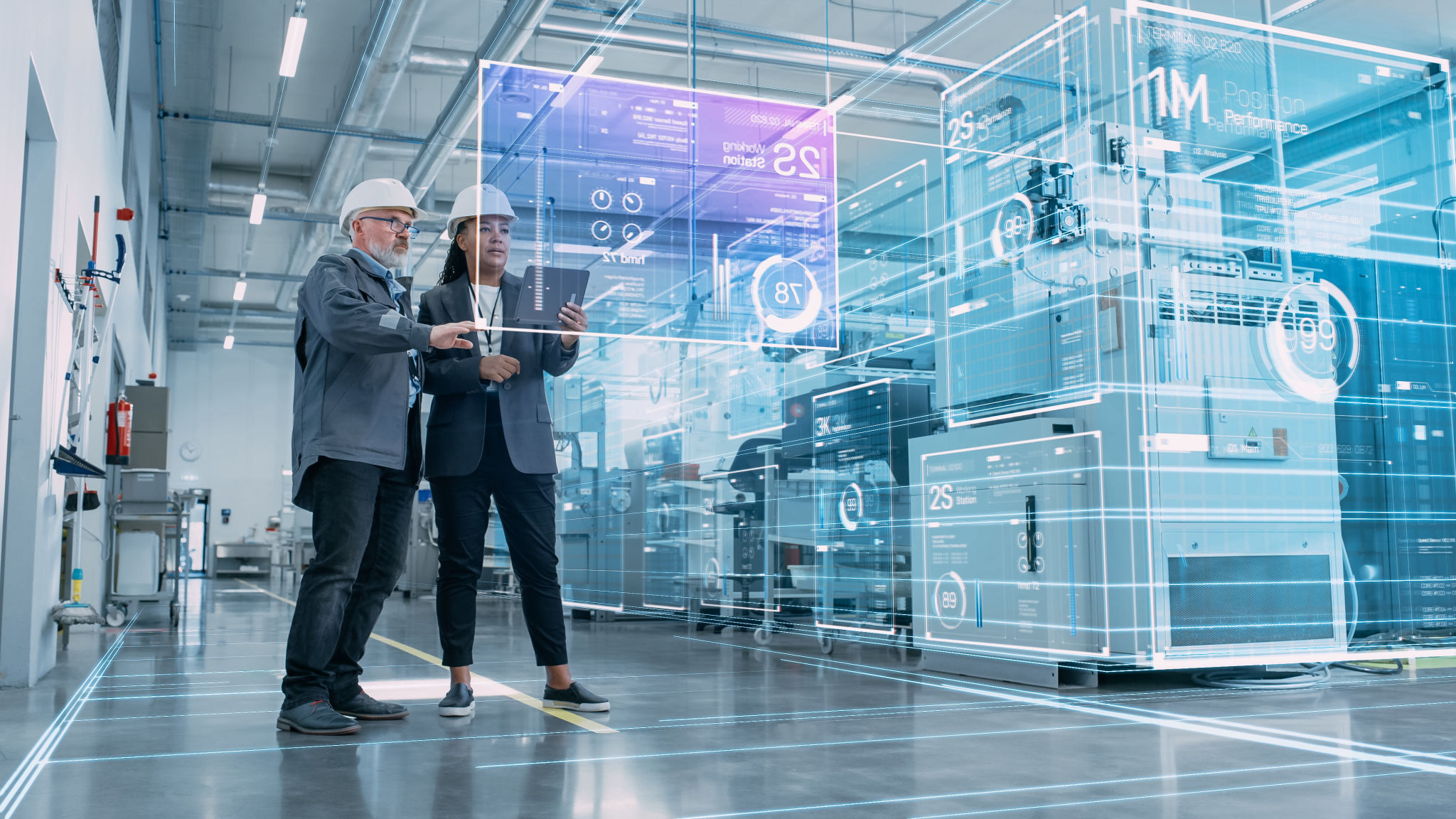
Technology Adoption
An essential component of the transformation was the adoption of cutting-edge technologies. The plant integrated IoT sensors that allowed real-time monitoring of equipment health, reducing downtime by predicting maintenance needs before failures occurred. Additionally, automation tools were introduced to streamline repetitive tasks, enhancing overall productivity.
Results and Benefits
The digital transformation yielded impressive results. Within the first year, the plant reported a 20% increase in operational efficiency and a 15% reduction in production costs. Improved data analytics capabilities enabled better forecasting and inventory management, while real-time monitoring enhanced equipment reliability, minimizing unexpected downtimes.

Employee Empowerment
A significant aspect of the transformation was empowering employees through training programs. By upskilling the workforce, the plant ensured that staff could leverage new technologies effectively, leading to increased job satisfaction and engagement. This empowerment played a critical role in overcoming resistance to change and fostering a culture of continuous improvement.
Conclusion
The successful digital transformation of this Georgia manufacturing plant serves as an inspiring example for other businesses in the sector. By strategically investing in technology and prioritizing employee development, the plant not only enhanced its operational capabilities but also secured a competitive edge in the marketplace. As industries continue to evolve, embracing digital transformation is no longer optional but necessary for sustained success.