Case Study: Successful Factory Optimization in Georgia Manufacturing
Introduction
In the competitive world of manufacturing, efficiency and optimization are key components for success. A recent case study on a factory in Georgia highlights how strategic enhancements can lead to remarkable improvements in production processes, reducing costs and increasing overall productivity. This case study serves as a blueprint for other manufacturing units aiming to achieve similar results.
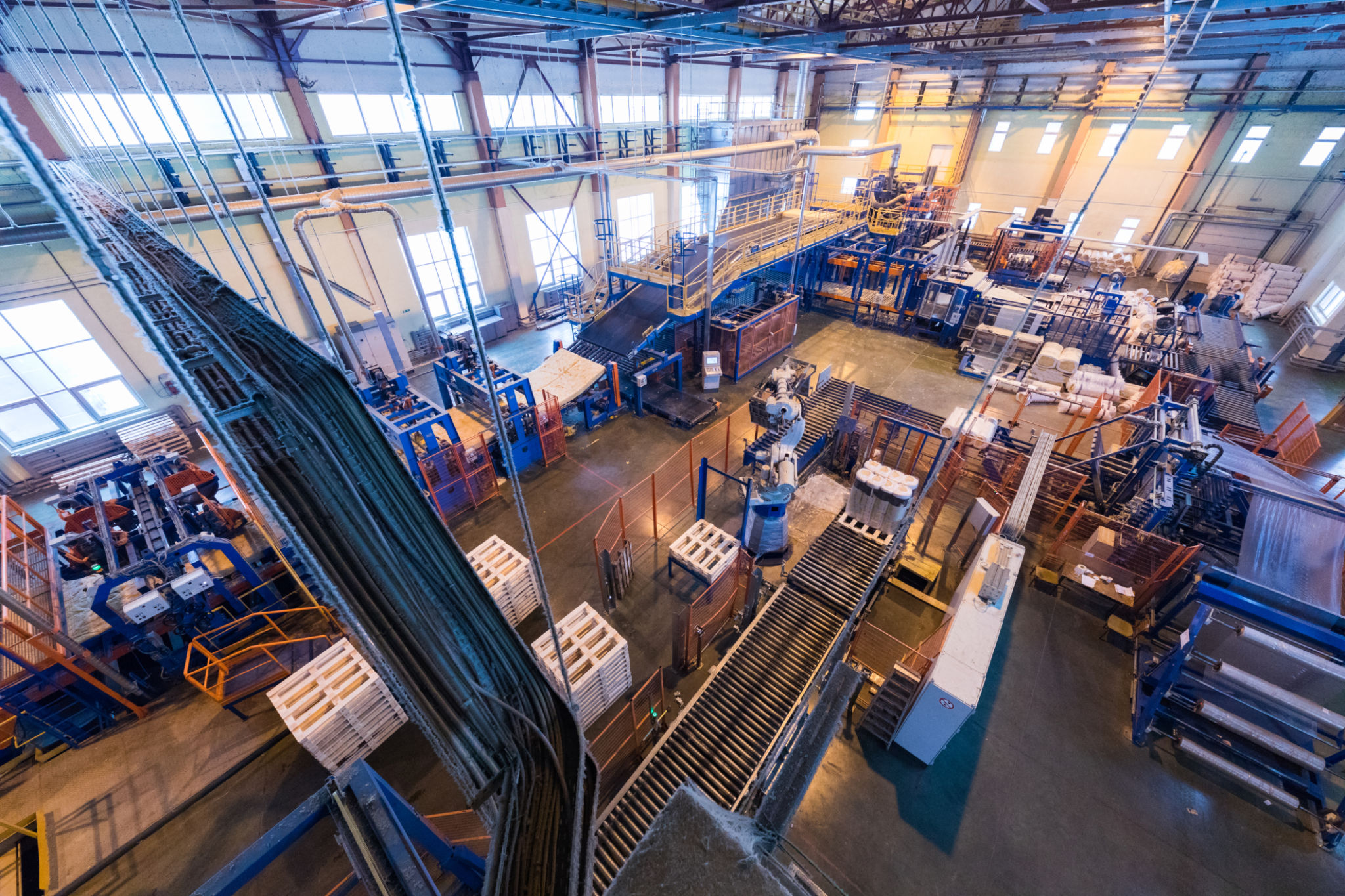
The Challenge
The Georgia-based manufacturing plant was facing several issues that hindered its operational efficiency. These included outdated equipment, inefficient workflows, and a lack of cohesive communication between departments. The management recognized the need for a comprehensive optimization strategy to overcome these challenges and set a new standard for productivity.
Identifying Key Areas for Improvement
The first step in the optimization process was identifying key areas that required immediate attention. The team conducted a thorough analysis of the plant's operations and pinpointed three primary areas for improvement:
- Equipment modernization
- Workflow restructuring
- Enhanced communication systems
Implementation of Solutions
Once the key areas were identified, the plant management embarked on implementing targeted solutions. They invested in state-of-the-art machinery that offered better precision and faster production times. This investment not only increased output but also reduced energy consumption, contributing to sustainability efforts.
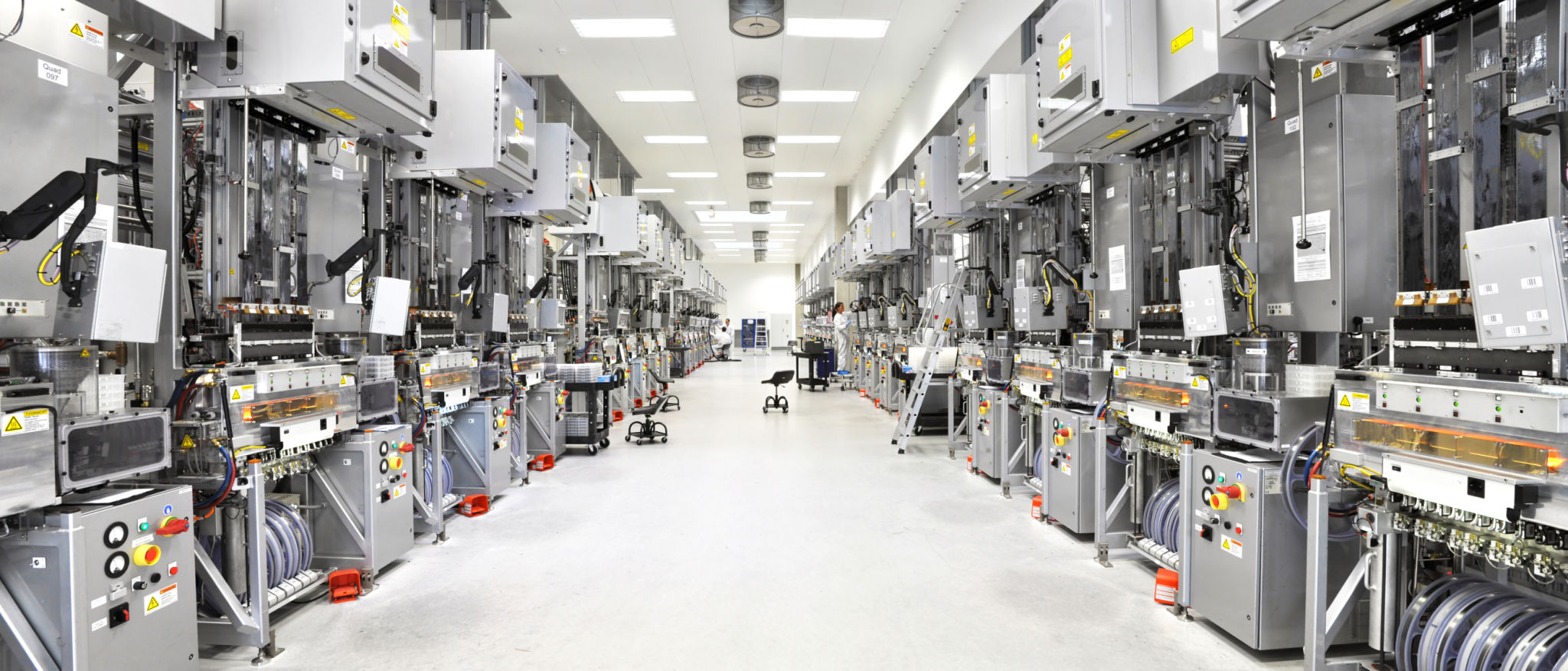
Restructuring Workflows
Restructuring workflows was another crucial aspect of the optimization process. By analyzing the production line, the team was able to eliminate bottlenecks and streamline operations. This restructuring involved reorganizing workstations, introducing lean manufacturing principles, and training staff to adapt to new procedures.
Enhancing Communication
Communication across departments was improved by implementing an integrated digital communication platform. This platform facilitated real-time updates and allowed for better coordination between teams, significantly reducing delays and misunderstandings. By fostering a culture of collaboration, the plant was able to operate more smoothly and effectively.
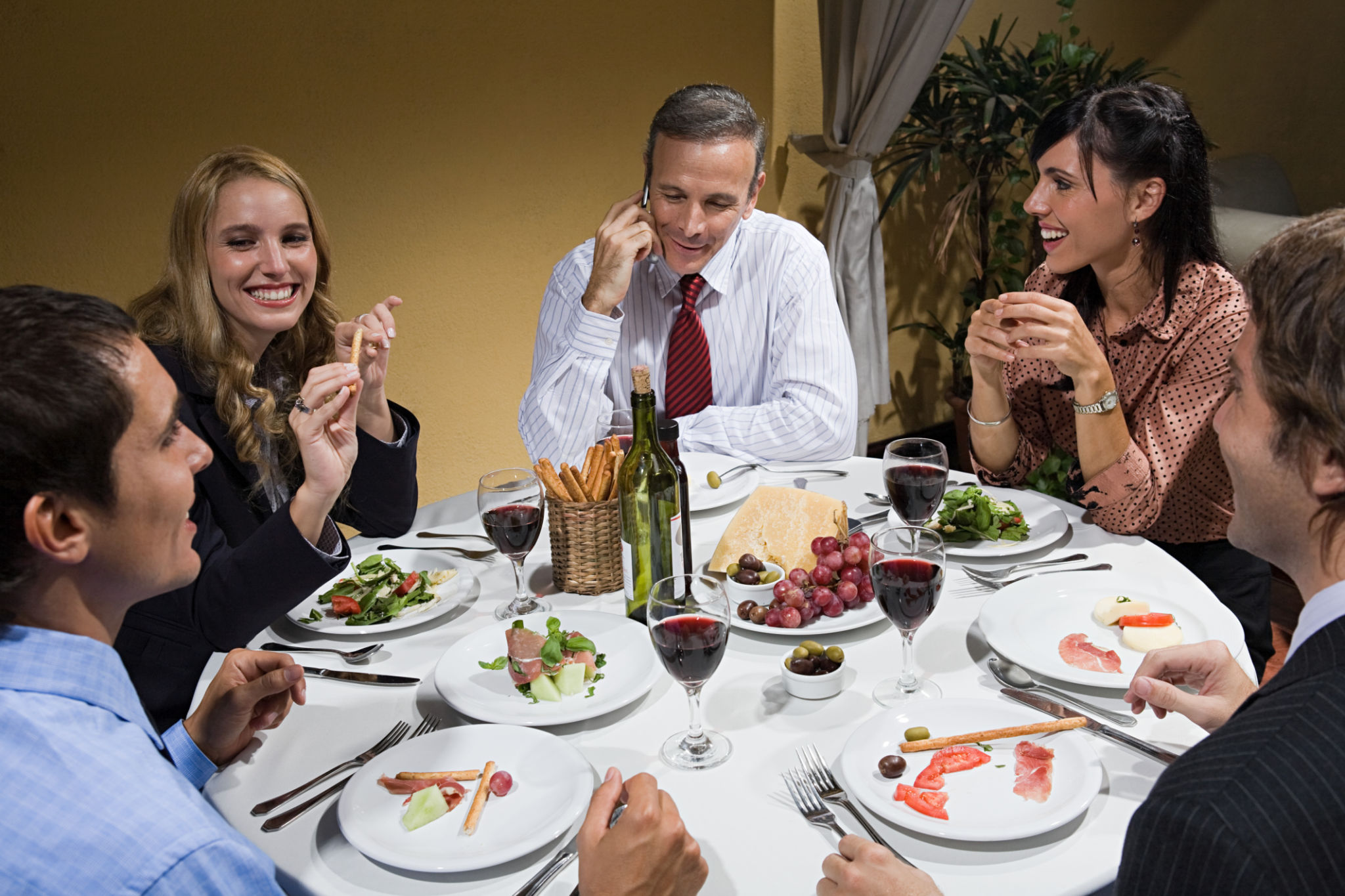
Measuring Success
The success of the optimization efforts was measured through various key performance indicators (KPIs) such as production volume, defect rates, and energy usage. The results were impressive: a 25% increase in production capacity, a 15% reduction in defect rates, and a 20% decrease in energy consumption. These metrics clearly demonstrated the efficacy of the implemented strategies.
Conclusion
The factory optimization case study from Georgia highlights the transformative power of strategic planning and execution in manufacturing. By focusing on equipment upgrades, workflow efficiency, and enhanced communication, the plant not only improved its operational capabilities but also set a benchmark for others in the industry. This success story serves as inspiration for manufacturing facilities worldwide seeking to enhance their productivity and sustainability.